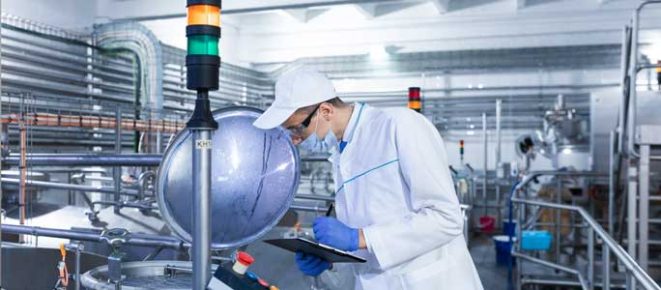
The tremendously vast & diverse pharmaceutical industry, under whose ambit fall drugs & vaccinations, pharmaceutical & medical devices, nutraceuticals, biotechnology, etc., is one of the world’s most highly regulated sectors with mandates impacting all the R&D, sample testing, clinical trials, product development, traceability, quality management, and reporting related activities in this industry.
The products in this industry are particularly scrutinized, because even the slightest of deviation in their quality can mean the difference between life & death, both literally and figuratively.
No wonder the pharmaceutical manufacturers are compelled to indulge in continuous innovation and follow closely monitored processes to develop and manufacture effective and reliable products that meet the strictest quality standards.
In such scenario, the pharma manufacturers, who in the past deployed old-school methods such as spreadsheets, manual and paper-based processes, and siloed stand-alone solutions, etc. for maintaining the regulatory requirements, today seek assistance of tools that support innovation, producing cost-effective yet quality drugs, and help maintain quality/hygiene standards, patient safety, and meet regulatory requirements.
With changing times and evolving needs, the regulatory requirements have only gotten more stringent. These requirements are subject to constant changes, and in no way can be tracked on paper or through manual processes anymore.
In modern times, enterprise resource planning (ERP) systems have emerged as that tool for pharma manufacturers.
But to survive and prosper in such business environment, pharma manufacturers need to meticulously assess and comprehend the ERP systems that keep a close check on the manufacturing, procurement, documentation and traceability — while cost-effectively managing compliance requirements.
In other words, the pharma manufacturers need to have pharma manufacturing software that should have got the testing and subsequent validation done; a software that is an integrated system which meets the business and regulatory needs by helping them get rid of the manual, error-prone methods, and meet all the local, regional, national, as well as international regulatory requirements, current Good Manufacturing Processes (cGMP) and Good Automated Manufacturing Practice (GAMP 5) norms, besides allowing them to record maintenance.
CGMP & GAMP 5
Before understanding software validation, we need to understand in brief what the cGMP and GAMP regulations mean.
The cGMP for pharmaceuticals contain minimum requirements for the methods, facilities, and controls used in manufacturing, processing, and packing of a pharmaceutical product, and the strength it claims to have.
The cGMP is concerned with both quality as well as production, and predominantly ensures that high quality products are produced on a consistent basis keeping the international standards in mind.
Its scope covers record keeping, hygiene & cleanliness, personnel qualifications, equipment verification as well as handling of complaints.
These regulations make sure that only those products which are effective and completely safe for consumption reach the end consumer.
Failure to comply with GMP regulations can have serious implications for the manufacturers, such as seizure, recall, fines and even imprisonment.
The nature of the pharmaceutical and other related industries requires that systems are developed, documented and tested following good engineering practices.
This is where the GAMP comes into the picture, defining best practices in specifying, designing, building, testing, qualifying and documenting the ERP systems to a rigorous validation procedure.
But what is software validation?
The need for software validation can be better understood by knowing about this process in its entirety, and also how it unfolds for the ERP software providers and their offerings designed for heavily regulated industries.
Software validation, also better known as ‘Computer System Validation’ (CSV), is nothing but the process which ensures that a software (or hardware) component meets its purpose in line with the regulatory guidelines for the given industry.
The process highlights the things missing in an FDA-regulated manufacturer’s computer system, which could ultimately impact patient safety, product quality and the pharma manufacturers’ brand reputation.
That is the reason why it is particularly important in FDA-regulated industries like pharmaceuticals, since products from these sectors can have sweeping effects on the health of the end consumer.
The entire process of CSV is created keeping in mind the FDA guidelines that have been defined for the pharma industry, in order to meet the quality standards and adhere to the pharmaceutical cGMP.
According to the FDA, software validation applies to all the ERP modules for the pharmaceutical industry that potentially affect the safety of an end user or patient.
This would include the modules of manufacturing, distribution, packaging, formula/recipe management, CRM, and Quality Control (QC).
For ex: In case of QC module, the FDA applies validation processes to functionality such as electronic signatures, recall/hold functionality, serialization/lot control — traceability features, Non-Conformance (NC) reporting, Corrective and Preventive Action (CAPA) reports, and Calibration and Test.
More so, in process industries, third-party validation of ERP software is an important process.
The purpose of third-party validation is to provide an objective review of the ERP software as a neutral party that is technically, financially, and managerially different from the organization doing the software development. Such validation confirms that claims made by ERP vendors regarding their products are fair and correct.
Why the need for software validation?
According to FDA guidelines, “A drug shall be deemed adulterated if: … the methods used in, or the facilities or controls used for its manufacture, processing, packing, or holding do not conform to or are not operated or administered in conformity with current good manufacturing practice …”. (FDA 21 CFR Part 211, 820). If a software is validated, it means the following:
- The organization’s products are in-line with FDA and global regulatory guidelines and meet all the FDA and cGMP standards.
- The products are absolutely safe for consumption. FDA has noted that ERP software validation is crucial to overall public health and safety. In the context of the pharmaceutical manufacturers, software validation’s objective is “to protect the public health by assuring the safety, efficacy and security of drugs, biological products and medical devices”, so that the manufacturers use cGMP and Quality System Management principles to comply with the law.
- The software has been set up properly and is configured for the documented processes outlined by the particular company.
- The software is useful for all the purposes it was intended for.
Advantages of software validation
Software validation has several advantages, such as:
- It helps the ERP vendors map their product development to the exact and accurate requirements of their customers who are pharmaceutical manufacturers.
- The validation process also helps the vendors pick up any possible flaws in the software that might have been missed during the verification phase.
- With a validated software, the pharma manufacturers are more likely to face a decreased failure rate, and fewer recalls.
- Validated pharmaceutical manufacturing software also helps organizations better manage and comply with audits.
- As stated above, software validation helps ensure compliance with pharma manufacturing standards. It helps pharma manufacturers ensure adherence to pharmaceutical cGMP guidelines, and maintain consistent quality.
To sum up
It must be noted that validated ERP systems help pharma manufacturers meet FDA requirements for software as well as operations.
So, looking for a pharma manufacturing software that has undergone successful validation and comes loaded with compliance monitoring, QC, and supply chain management functionalities, among others, should be a no-brainer for the pharma manufacturers.
BatchMaster has been offering pharmaceutical manufacturing software successfully for over three decades now. Its solutions are flexible enough to accommodate future opportunities, adept enough to address both current and future regulatory mandates, and importantly, validated by an independent third-party.