Best ERP Software for Paint Manufacturing
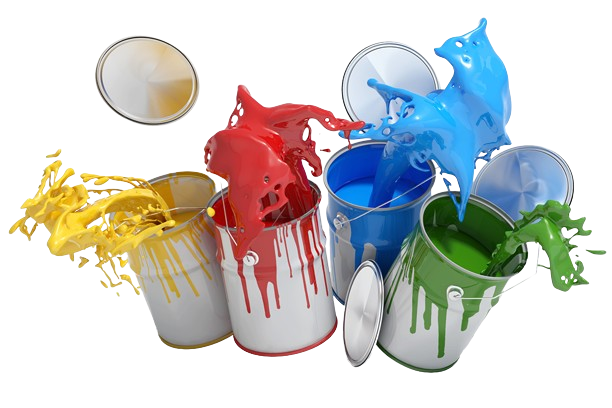
Why Your Paint Manufacturing Business Needs BatchMaster ERP?
The paint manufacturing industry faces challenges such as fluctuating raw material costs, regulatory compliance, and inventory management complexities. Staying competitive while ensuring efficiency, product quality, and sustainability requires the right technology.
BatchMaster Paint ERP is a specialized solution designed to streamline operations, enhance supply chain management, and automate daily tasks. It helps paint manufacturers overcome industry challenges, drive innovation, and stay compliant with ever-changing regulations.
With BatchMaster Paint ERP, you can:
- Regulatory Compliance: Easily generate GHS reports, Safety Data Sheets (SDS), and other regulatory labels through LISAM integration.
- Enhanced Traceability: Barcode and RFID-enabled lot management provide complete traceability from raw materials to final products.
- Financial Integration: Seamlessly integrates with systems like SAP Business One, QuickBooks, Sage 50/100/200/300, and Tally.ERP 9 for smooth financial management.
Upgrade to BatchMaster ERP system for the paint industry to streamline your business, ensuring efficiency, compliance, and product quality.
Experience the Power of BatchMaster Paint ERP Software
Paint Industry
Industry Sectors
Capabilities Offered by BatchMaster ERP for Paint Industry
BatchMaster paint manufacturering ERP offers various capabilities to paint manufacturers, like:
- Vendor Validation: In the paint industry, raw material quality and consistency are crucial. Variations in pigments, solvents, or ingredients can greatly impact the final product. Our paint ERP software ensures product consistency by offering a robust vendor validation system, simplifying the management of certified vendors who meet required standards for raw materials.
- Formula Consistency: Maintaining high-quality results is essential in paint manufacturing. Even slight variations in ingredients can affect the product’s quality. ERP for paint industry addresses this challenge by offering multi-level formula specifications, flexible unit of measure (UOM) structures, automatic UOM conversions, and precise product quantities (up to six decimal places), ensuring consistent formula output.
- Formula Management: Paint ERP system leads the industry in formula management, providing advanced controls, security, version control, and formula comparison capabilities. Manufacturers can create, manage, and approve multiple formula versions while maintaining only the active, approved formula for production. This ensures accuracy and consistency in every batch.
- Barcode & RFID-Enabled Lot Management: With integrated Barcode and RFID-enabled lot management, BatchMaster Paint ERP offers end-to-end traceability, enabling manufacturers to track raw material lots from their source to the production line. This feature enhances visibility and control across the entire supply chain.
- Regulatory Compliance: Paint manufacturing ERP integrates seamlessly with LISAM to generate Globally Harmonized System (GHS) reports, Safety Data Sheets (SDS), and other labels in compliance with legal regulations. This ensures that your manufacturing processes meet all required standards.
- SuperBatch: Simplify your production process with BatchMaster’s innovative SuperBatch feature. This capability allows you to merge intermediate and finished goods batches into a single batch in chronological order, improving efficiency and reducing production complexity.
Transform Your Paint Business with BatchMaster ERP
Unlock Predictive Insights, Drive Success, and Achieve Amazing Results!
Benefits of ERP Software for Paint Manufacturing
The benefits of ERP software for paint manufacturing are numerous and can significantly enhance the operations and competitiveness of your business. Here's an optimized list of these advantages:
Paint ERP streamlines operations, enhancing efficiency and productivity while promoting safety measures throughout the paint and coatings supply chain.
Advanced data management and analysis capabilities provided by ERP system improve research and development (R&D) productivity, enabling data-driven decision-making and innovation.
ERP software supports the development of innovative solutions and helps you stay at the forefront of the industry by facilitating research, development, and experimentation.
With efficient processes and data management, ERP accelerates product development, allowing you to bring new products to market more quickly.
Delivering high-quality products on time improves customer satisfaction, contributing to a loyal customer base.
Consistently meeting customer expectations with quality products and on-time delivery can help you build a loyal and expanding customer base.
ERP system for paint manufacturing supports quick scalability of production to meet changing market demands and opportunities.
Efficient data management and integration ensure a seamless flow of information across various departments and processes.
ERP for paint industry simplifies complex formulation processes and provide secure management of formulas, ensuring consistency and quality.
At all stages of production, ERP software helps optimize and enhance manufacturing processes, increasing operational effectiveness.
ERP for paint manufacturing helps you stay compliant with stringent governmental and environmental regulations, reducing the risk of non-compliance issues.
By implementing ERP software for paint manufactruing industry, you can experience these benefits, leading to enhanced operational efficiency, customer satisfaction, and overall competitiveness in the industry.
Key Features of ERP Software for Paint Industry
Paint ERP Designed to Meet GHS and SDS Requirements.
- Formula Security with Revision Controls
- Easy Reformulation Options for Product Development
- Separate Formula costing
- Separate Product Costing
- Lot Potency Calculation Support
- Sample Management
- Quotation Management
- GHS Compliant SDS Reports & Labels
- HAZMAT Bills of Lading
- VOC & SARA Reporting
- Bi-directional Lot Traceability
- Vendor Qualification and Management
- Quality Control as per cGMP Guidelines
- HMIS/WHMIS Support
- Non-Conformance and CAPA
- Complete Tracking and Accountability of Disposed By-products
- Customizable COA (Certificate of Analysis) Reports
- Warehouse Management
- Shelf Life/Expiration Dates
- Supports Multiple Units of Measure
- Containerization
- Make-to-stock and Make-to-order Operations
- Robust planning
Run Our Manufacturing ERP With Your Existing Financials
Upgrade to our ERP without missing a beat in your financial and accounting routines. BatchMaster ERP offers seamless integration with Tally, QuickBooks, Sage 50/100/200/300, SAP Business One and other popular systems, ensuring a smooth transition.
Web/Cloud Deployment Available
Give your small, mid-size, or large-scale businesses the power of our ‘Cloud ERP’ solutions, and enjoy the benefits of leveraging the cloud.
Looking To Find Best Solution for Your Business?
Allow our expert team of solution consultants to review your business operations so that they can offer you the best-possible solution, either on premise or in the cloud, to meet all your industry-specific needs