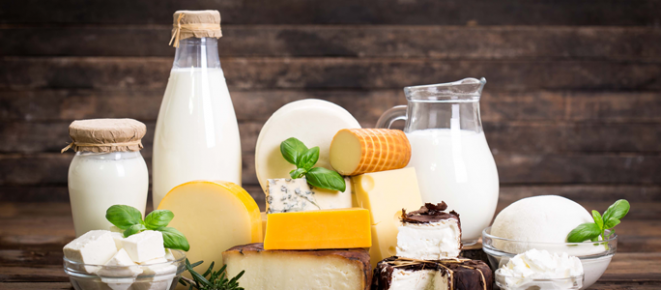
We live in times where good taste is not the only thing that consumers seek from the food products they buy.
These days, the issues pertaining to food safety & quality as well as product ingredients have taken the center-stage.
Majority of food & beverage manufacturers today ensure the products they offer are rich in taste and nutrition, which means the consumers have shifted their focus to a new must-have product attribute, which happens to be trust.
In almost all the sub-sectors of the food & beverage industry, including the dairy businesses, there is consumer distrust brewing, and there is a great level of concern.
Today, many consumers make food & beverage manufacturers uncomfortable by asking a lot of questions about a product—right from its ingredients, place of origin, and impact on the environment to working conditions.
A lot of factors such as the outburst of food-borne diseases, guarded manufacturing techniques, and well-publicized food scams on a global level – case in point being the melamine scandal – are to be blamed for it.
This means that despite making remarkable progress in terms of production, quality inspection, meeting stringent regulatory requirements, and despite more and more manufacturers explaining how they source and make products, the dairy manufacturers fail to retain a substantial number of consumers’ trust in their offerings.
In such times, it has become vital for dairy manufacturers to revisit their processes and ensure their transparency and safety.
Through this blog, let’s take a look at the reasons that have predominantly led to the consumer distrust in dairy products, and also at ways through which dairy ERP systems can help the dairy businesses earn back that trust.
Reasons behind distrust
Food labeling is a critical area of contention in the dairy industry. The modern-day consumers demand accurate product information in order to make informed choices.
However, the same consumers often express a lack of trust towards the accuracy of labels due to reasons such as inconsistency or information overload.
They are unsure whether the products they are purchasing are safe to eat, and have been prepared without affecting animals or nature.
It is thus important for the dairy manufacturers to provide accurate and relevant information to the consumers at the time of purchase.
In the big, diverse dairy industry, just as any other food manufacturing industry, the chances of contamination are pretty high, and this is yet another area of contention.
There are organized crime networks that deliberately dilute, adulterate, mislabel, and substitute food & dairy products.
Such acts impact on sustainability, nutrition, and even social responsibility, affecting animal welfare and human rights.
This is something which has become increasingly important to consumers over the years.
In such markets, where consumers can’t distinguish between sellers of good products and contaminated products, this can result in consumer losing trust in the entire category.
Long and complex supply chains are yet another reason behind the consumer distrust. The longer the supply chain is, the more prone it is to disruptions.
Today the consumers want to know where the products they buy are coming from, but the food retailers find it difficult to determine where the ingredients are sourced from or how they are processed or handled.
This lack of visibility into the supply chain creates significant gaps in the business’ customer and risk management structure, leaving them exposed to potential legal, financial and reputational damage, which may result in consumer distrust.
With an extremely short shelf-life, the dairy products need to be handled under special conditions like temperature, packaging, etc.
Absence of which leads to products getting ruined and thus wastage. This is another reason in the hit-list of customer distrust.
They expect some way by which milk and other milk products travel greater distances while remaining fresh and having the required shelf life after arrival at their destinations.
Managing shelf life and expiries have therefore become an important aspect for dairy producers.
How ERP can help repair relationship with consumers?
To begin with, manufacturers need to make their consumers believe that they are doing things the right way.
They need to be transparent about their production processes, as it is linked directly to trust. Consumers world over are preferring the food brands that are more transparent about their production processes.
This is exactly why companies today are investing in dairy ERP solutions, which support product labeling.
Manufacturers, through product labeling, are nurturing consumer trust and eventually generating more revenue.
These labels share vital product-related information desired by the consumers such as, details about the ingredients used, allergens present, additives, preservatives and artificial flavors used, manufacturing and expiration dates, GMO ingredients, Manufacturing, transportation and packaging processes, lot size and lot number, shelf life, etc.
All the major dairy ERP solutions support product labeling, and subsequently help dairy manufacturers retain the consumers’ trust.
Moving forward, ERP for dairy industry helps dairy manufacturers uphold production standards and maintain high levels of regulatory and quality control (QC), which eventually allows the dairy manufacturers achieve quality customers expect, less waste, increased efficiency, and greater overall sustainability.
An ERP for Dairy ensures all of this through its QC module, as it puts in place proper quality checks, and allows the dairy manufacturers to instantly monitor each step of the production process to see whether the checks have been completed or not.
Additionally, it also helps track data pertaining to quality and compliance in real time thus, helping the dairy manufacturers take proactive actions and deliver only the best quality products that curb customer’s distrust.
An ERP for the dairy industry also gives the dairy manufacturers as well as other stakeholders an end-to-end, complete picture of the supply chain, or in other words, helps create a fully transparent and traceable food supply chain.
This means that they know how a product develops from concept to consumption, including visibility of the people, places and processes involved.
It allows dairy manufacturers to track the movement of their different products throughout the different stages of production, processing and distribution by recording and proper documentation.
Traceability has many benefits to dairy & food businesses specifically in case of recalls, as it helps minimize the impact of contaminated products by helping in identifying and removing the defected lot at a much faster pace.
This also brings into kitty many other benefits such as improved operational efficiency, assured quality, better brand reputation, decreased risk of legal issues, and customer trust, among others.
Conclusion
Winning back a disgruntled customer, or regaining his trust is never an easy job. It takes best manufacturing practices, complete adherence to quality, safety, and regulatory requirements, end-to-end traceability in the supply chain, and accurate product labeling, among other things, to win and retain consumer’s trust.
Most dairy businesses are aware of the utility of an ERP for the dairy industry in achieving the aforementioned.
If you are also into a dairy business, and looking for ways to nurture customer trust, we at BatchMaster can help you. Write to us at sales@batchmaster.com today.