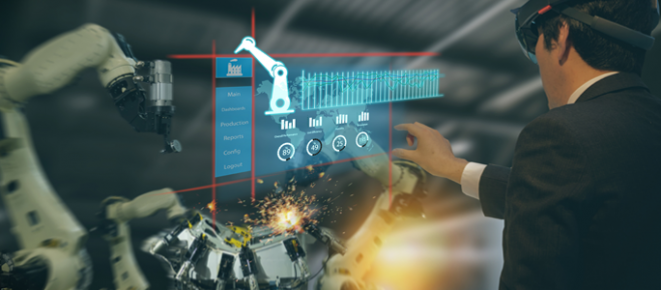
When we hear or read about the term industrial revolution, we are invariably teleported back in time to our high school days, when we learned about it for the first time.
Back then, our Social Science text books would tell us how the first industrial revolution in the 18th century resulted in the mechanization of the manufacturing industry- the textile industry in particular.
It marked the birth of the factory, and shift from human labor to machines through the use of water and steam power.
Then came the second industrial revolution in the early 20th century, and introduced us to the moving assembly line and propelled the growth of mass production with the use of electrical power.
We read how these revolutions made people richer and created more urban areas.
Around the same time, the third industrial revolution driven by electronics, information technology, and automated manufacturing was silently happening around us, and the manufacturers were going digital.
All this while, we perhaps never thought that we will get to witness another industrial revolution in our lifetime. And here we are, standing at the cusp of it. The fourth industrial revolution or Industry 4.0 is making waves, and many countries across the globe are adopting it.
What exactly is ‘Industry 4.0’?
Going a step further from the third industrial revolution, the fourth industrial revolution, or the Industrial Internet of Things (IIoT), or simply Industry 4.0, is going to be an amalgamation of all the latest technologies and manufacturing, where the machines, particularly at the shop floor, will be equipped with the ability to communicate so as to achieve visibility over every aspect of the operations, including goods, assets, and processes.
Facilitated by the rapid developments that have happened on the information technology and hardware front, Industry 4.0 is nothing but a blend of advanced analytics, Big Data, Robotics (machine learning), Artificial Intelligence (AI), Internet of Things (IoT), Blockchain, Radio-Frequency Identification (RFID) systems, Real-time Locationing Systems (RTLS), 3D printing, and Process Digitization across the business value chain, thus leading to a convergence of real and the virtual world.
Also being referred to as ‘smart factory’ or smart manufacturing, the concept of Industry 4.0 is going to change the way manufacturing happens across the globe by completely digitizing the manufacturing sector.
The fourth industrial revolution has in fact already begun and is redefining traditional manufacturing operations, simplifying things by streamlining processes, reducing human labor, making the supply chain more transparent, and opening the doors for unlimited possibilities.
It is being touted as the future of manufacturing, and it won’t be long before the manufacturers world over realize its potential.
Industry 4.0 in Modern India
We live in an era where technological innovations and changes are happening around us at a rapid pace. The fourth industrial revolution aka Industry 4.0 is a result of the same.
Businesses don’t want to be left too far behind in the race and hence are fast embracing the technologies we spoke about in this blog earlier.
The concept of a ‘smart factory’ with connected manufacturing units is fast becoming a reality everywhere – including India.
Diverse businesses in the country, be it the startups, SMEs or big corporations, are opening up to the idea of Industry 4.0.
With manufacturing machines getting more connected than ever, the manufacturers are looking to invest in efficient manufacturing infrastructure and making tangible improvements in efficiency, safety, profitability and performance.
In fact, quite a few manufacturing companies in India have begun implementing the power of Industry 4.0 in their operations.
For example, some manufacturing factories have started using advanced data analytics and autonomous robotics in some form or the other.
They are also using technologies like RFID to connect their factories from end-to-end, and gain more information such as detailed work instructions, bill of materials, and tracking numbers, etc.; and also RTLS, to collect critical data about assets including location, stage, and condition.
The manufacturers are gradually looking to build a framework for intelligent manufacturing plants that connect with every machine at the shop floor and keep a tab on the efficiency and work, so that they can bring down the waste substantially, and improve production processes.
Technology is helping them in this quest, as using advanced analytics, the manufacturers can enhance production capacity and its quality; through data analytics, they are using preventive measures to remove the defects; through robotics & automation, they are shortening the production cycle; and reducing time-to-market; through IoT, they are tightening the supply chain and reducing lead times; and through digitization of various business processes, they are creating a business model which is cost-effective and offers better experience to customers.
The challenges that lie ahead
However, as is the case with any technological revolution, Industry 4.0 too has its own share of challenges that need to be addressed by the Indian businesses. Perhaps the biggest of them all is related to the creation of relevant infrastructure for Industry 4.0.
World Bank data reveals 15.5 percent population of India still does not have access to electricity. Also only 26 percent of its population has access to the internet.
This is a massive challenge as the country with such less penetration of electricity and the internet can’t be ushering in the era of Industry 4.0.
The fourth industrial revolution is also likely to have massive implications for the jobs and the employees, as heavy use of AI and robotization, and introduction of more and more automation will take away more human jobs than ever. Any job that will require minimal or no human intervention is going to be affected.
However, automation will also create new demand for highly-skilled knowledge workers, which in turn will prove to be a challenge for the manufacturers.
For the fourth industrial revolution to well and truly arrive in India, there will be a requirement of skilled manpower, and the manufacturing companies will need to invest in upskilling talent within factories, and capability building as well as cultural change.
Upskilling in areas of analytics and digital technologies will prepare the workforce for the changing environment and also keep them relevant.
There’s also the challenge of creating a robust infrastructure for enterprise IT or ERP systems to adapt to changing business systems and processes.
How India can get ready for Industry 4.0?
All the challenges notwithstanding, Industry 4.0 has proved around the world that the business processes can be improved without really shedding jobs.
It has made businesses more competitive than they have ever been, resulting in lower prices for consumers, higher wages for employees or higher profits, leading to increased demand and more jobs.
That’s precisely why it is important for businesses to get ready for the fourth industrial revolution.
The Indian government under the leadership of Prime Minister Narendra Modi too is playing its part in getting the country ready for Industry 4.0.
Efforts are being made to upgrade the IT infrastructure, and the infrastructure in general, and strengthen the manufacturing sector by using the latest technology and material.
Through programs like ‘Make in India’, ‘Digital India’, and ‘Skill India’, the government is looking at job creation and skill enhancement in different sectors of the economy, and transforming India into a global design and manufacturing hub; improving online infrastructure and increasing internet connectivity; giving vocational training to millions of youth in partnership with the corporate sector, and also imparting training at grassroots in universities through specialized curriculums.
The ‘Skill India’ initiative is thus closely linked with the success of Industry 4.0 in India.
However, there’s still much more to be done. There is a need to make progress in areas such as cognitive robotics, advanced automation, and other streams of qualitative skills.
With more human-machine-cooperation and engagement coming into play, there is a need to develop safety-related capabilities. Lastly, there is a need to create robust security infrastructure for the practical application of the ‘Smart Factory’.
The government too should play its part in enforcing tight regulations for data protection and security, and building a mechanism to manage advanced targeted cyber-security threats and attacks.
But before that Government should ensure regular flow of electricity and Internet services in every corner of India which stands as the basic requirement to adopt Industry 4.0.
Conclusion:
Industry 4.0 is a reality the Indian manufacturers will have to come to terms with sooner rather than later.
Luckily, the process manufacturers in India and abroad have a seasoned partner in BatchMaster Software Pvt. Ltd. that can help them build an ecosystem that supports the Industry 4.0 revolution, and help them understand and implement modern generation ERP systems, so that they can survive and thrive with the Industry 4.0.
Get in touch with our team of experts to know more about a successful ERP implementation for your industry, or for a free demo.