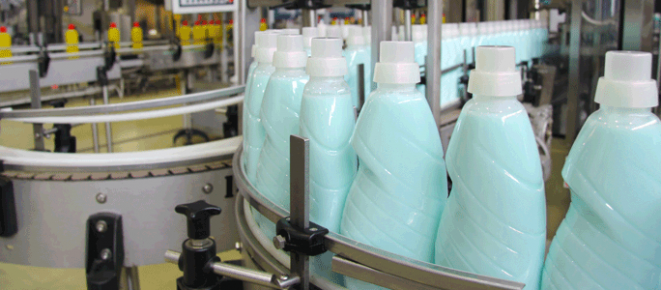
You might be an established player in the manufacturing business, or maybe you have just started out and are new to manufacturing.
Whoever you are, you must surely have come across the term Bill of Material, or simply “BOM”, on a frequent basis.
A BOM is an essential component of the manufacturing process that binds together all the concerned departments and suggests how a product should be put together.
A BOM is vital part of the manufacturing process for both discrete as well as process manufacturers. Talking particularly about the latter, a BOM has great importance.
It allows linking the formula with the finished goods or the intermediates stored in the inventory.
A BOM is important. An incorrect or incomplete BOM can result in:
- Lower material planning
- Material shortages
- Incorrect product costing
- Raised production costs
- Costly delays in shipments
- Lost sales – or even bring the entire unit to a standstill.
This is precisely why the manufacturers must fully understand exactly what a BOM is, how it functions, what its types are, and why the Bill of Materials is important.
What is Bill of Materials?
Bill of Materials is nothing but an organized list of all the components that make up a product or assembly, including:
- Raw materials
- Semi-finished products or ingredients
- Sub-assemblies
- Intermediate assemblies
- Sub-components
- Parts
- Material number of each component
- Unit of measure
- And the quantities of each needed to manufacture an end product.
A manufacturing BOM may be used for communication between manufacturing partners or confined to a single manufacturing plant.
It defines how an item is manufactured from top to bottom.
It informs everyone involved in procurement and manufacturing chain about what to purchase, how to purchase and where to purchase.
A BOM can be a single level and multi-level. You can understand it this way.
A finished material can contain semi-finished materials as components, which in turn can have raw materials as components in the next level.
A manufacturing BOM also includes a full set of instructions on how a product must be assembled right from the conception phase through to the finished product ready for shipping.
It contains list of packaging materials also.
A well-defined BOM can help manufacturing businesses with:
- Planning for purchases of raw materials
- Estimation of the material costs
- Enhance inventory control
- Tracking and planning material requirements
- Maintaining accurate records
- Waste reduction etc.
Type of BOM in BatchMaster ERP:
– Container BOM:
The container BOM is mostly used by bulk manufacturers. It can be explained this way: A Cola manufacturer produces 10,000 ltrs. of Cola and stores it in bulk.
He then sells it in different packs of 200 ml, 500 ml, and 1 ltrs., 2 ltrs. etc. The manufacturer can’t do it without using a container BOM.
– Intermediate BOM:
The intermediate BOM also links formula to an item, but in this type of BOM, no packaging is required for an intermediate item.
– Finished Good BOM:
A Finished Good BOM links formula to an item. In this type of BOM, the packaging items and their quantities are also defined.
– Assembly BOM:
An assembly BOM is predominantly used for discrete items, and it allows the assembling of the final product.
Another important part of a BOM is its Fill Level.
It basically signifies the quantity of the material that should be filled to make one stock unit of the end item.
BOMs provide manufacturers with the flexibility to define Fill Level in the desired unit of measurement.
It can be interpreted in the system weight unit or system volume unit.
This eventually helps in meeting the current yet an important requirement of multiple packaging by the manufacturers.
For a Finished Good BOM, the material to be filled is produced using the formula associated with this BOM.
Fill Level is not applicable to an Intermediate BOM, as an intermediate is not a packaged product.
Also, Fill Level may be assigned for an Assembly BOM too, allowing cost analysis.
Why is the Bill of Materials important in manufacturing?
By now you must have got a fair idea about how critical a role manufacturing BOM plays in the development of any product.
In fact, you simply cannot manufacture a product without a BOM. It helps the process manufacturers manage and oversee resources and identify materials to reduce wasteful spending.
It does it by providing accurate information.
This facilitates better decision making to manufacture cost-effective & efficient products. – irrespective of whether they are food products, pharma products, chemicals, or paints.
Let’s look at exactly why Bill of Materials is so important in manufacturing:
– Avoid running out of materials:
Due to inaccuracy in BOM, the production team runs out of inventory required to build the product, thus resulting in production halts.
With a clear list of materials, quantities and inventories, a manufacturing BOM allows you to manage what you need to ensure you never run of materials again.
An ERP software, which allows you to set reminders when stock is running low, also comes in handy in this regard.
– Get a tailor-made shopping list:
With knowledge of exact requirement of raw material and its quantity, procurement of materials becomes low lying fruits for the manufacturers.
BOM offers the manufacturers a tailor-made shopping list. Depending upon budget you can scale up or down this list.
– Ensure better planning:
Quite similar to the point mentioned above, BOM offers a comprehensive list to the process manufacturers.
This list may contain what is needed to complete a project.
This way, the planners are equipped with all the data they require to chart out a plan. Like how long the project will take and how many people need to be involved.
– Time & cost savings:
Since a manufacturing BOM lays the foundation for effective inventory management, the manufacturers can ensure the stock is ordered only when it’s required.
This way, manufacturers can reduce inventory holding cost.
Furthermore, with the knowledge of how much of each component is required, and with individual components being in stock and waiting to be used, manufacturers save crucial time.
They also save time by linking one formula to multiple BOMs.
– Uplift consistency:
There are many small businesses where often only one person is responsible for specific areas of production. For such businesses, a manufacturing BOM provides a framework.
This framework can be followed by the staff to ensure consistency.
– Unites all departments:
A Bill of Materials primarily ensures that all departments work together as one.
Different departments such as design, procurement, production, and sales give input to ensure that the created BOM is 100 percent accurate.
– Convenience:
The packaging of finished goods is often done keeping the convenience and the requirements of the end consumer in mind.
For example, packaging may range from an 8-gm sachet, to 250-500 gm bottles, to bulk containers.
In such a case, using a BOM, a manufacturer can associate formula, labor, overheads as well as packaging materials with the finished good to govern the production process.
Conclusion
If you’re looking for advice about a manufacturing ERP software or creating Bills of Materials for your process manufacturing business, please contact our sales team.
You can reach out to the team at sales@batchmaster.com.
We’re confident your search will end at BatchMaster ERP. BatchMaster ERP is a specialized manufacturing ERP with a comprehensive BOM functionality.