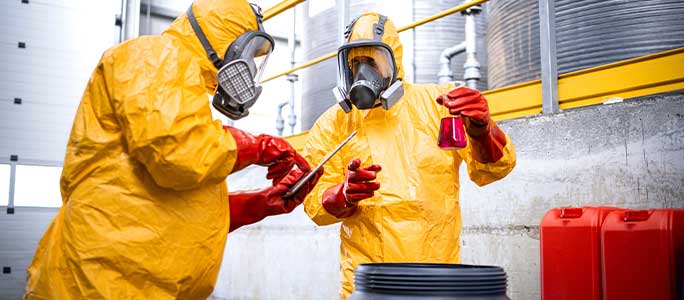
Overview-
“Prevention is better than cure.” We all are very well familiar with this old-age proverb that suggests us to take necessary preventive measures while performing high-risk tasks. To make it simpler, consider a case of you performing any of the daily household chores that carry risks.
Whether you have to handle and move a vessel full of boiling water, or have to take your dish out of oven that you microwaved, either you will use a piece of cloth or a pair of hand gloves, to prevent yourself from getting scalded.
This is what today’s blog topic is all about—safe handling, managing, and storage of those numerous hazardous materials that are being used across a wide range of manufacturing industries including, chemical manufacturing, pharmaceutical manufacturing, paints & coatings manufacturing, etc.
Role of Hazardous Materials in Manufacturing Operations
Industries that use highly concentrated materials during the manufacturing process, need to adopt all the necessary safety measures while staying compliant with some industry-specific regulations.
If the manufacturing is on a small scale and involves only one or two hazardous materials that are not highly concentrated, then executing safety and compliance procedures manually will work.
But executing large-scale manufacturing, that involves numerous highly concentrated and hazardous materials in large quantities, makes the execution of safety and compliance processes a tough task for manufacturers.
This is where an ERP software for hazardous materials comes into play and lightens the burden. But before that have a look at the different manufacturing sectors where hazardous materials play a crucial role.
Chemical Manufacturing:
Manufacturing of chemicals such as fertilizers, industrial solvents, and adhesives involves hazardous materials such as benzene, chlorine, sulphuric acid, etc.
Food Manufacturing:
Some food processing operations require controlled use of hazardous materials like ammonia for refrigeration or cleaning purposes.
Pharmaceutical Manufacturing:
Manufacturing active pharmaceutical ingredients often involves hazardous substances such as methanol, acetone, formaldehyde, etc.
Cosmetics Manufacturing:
A list of hazardous materials including formaldehyde, parabens, dyes, and certain preservatives are used prominently in cosmetics manufacturing.
Paints & Coatings:
Numerous highly hazardous solvents, pigments, and additives are used in manufacturing paints & coatings such as toluene, xylene, lead compounds, etc.
Although these materials are indispensable for production, manufacturing firms need to adopt tightened safety protocols while handling and managing them—preventing workers, consumers, and the environment.
Have a look at how ERP software for hazardous materials helps manufacturers implement a robust policy & maintain the utmost safety across the workplace.
Centralized Compliance Management-
Regulations governing hazardous materials vary across regions and different industries. ERP software simplifies this by
- Staying updated with current regulations such as
Safety Data Sheet Management (SDS)-
Safety data sheets provide crucial information regarding the potential chemical hazards that are being used in the workplace and the risks they pose.
ERP for chemical manufacturing enhances SDS management by
- Generating, digitally storing, and organizing SDS for easy access by employees and stakeholders anytime.
- Updating SDS automatically, ensuring they remain compliant with changing regulations.
- Integrating SDS into workflows, enabling workers to access safety information for safe handling and storage processes.
Incident Reporting & Emergency Response Planning-
In the face of an emergency, timely response is of great importance to minimize the loss. Specifically, in chemical manufacturing, events like unexpected emissions, sudden changes in storage conditions, accidental release or leakage of hazardous chemicals, cross-contamination of chemicals, etc., demand immediate attention & response.
Chemical Manufacturing ERP Software helps in this regard by
- Enabling the creation of detailed emergency response plans, including step-by-step actions, contact information for responsible personnel, and critical resources.
- Enabling collaboration across teams through centralized data & communication tools
- Offering pre-defined emergency response plans tailored to specific scenarios.
Inventory Classification-
Proper classification of hazardous materials is vital for compliance and safe handling, preventing accidents and adverse reactions. ERP software for chemical manufacturing helps in this regard by:
- Categorizing materials based on hazard levels, chemical properties, and storage requirements.
- Labelling inventory with appropriate symbols and handling information.
- Enabling quick identification of materials during emergencies or audits based on their classification, location, and potential risks they pose. For example, flammable substances can be identified and isolated quickly in case of fire hazards, while toxic substances can be flagged for containment to prevent exposure.
Labelling & Packaging-
Proper labelling and packaging becomes extremely crucial when dealing with such hazardous chemicals. It helps manufacturers ensure safety, compliance, and effective handling.
Chemical ERP software simplifies this process by:
- Automating label generating with hazard symbols, barcodes, and required regulatory information mandated by GHS, OSHA, REACH, etc.
- Providing detailed guidelines to ensure products are packed securely to prevent leaks, contamination, or exposure.
- Enabling real-time tracking of materials throughout their lifecycle by linking the barcodes with the ERP system.
Proper Disposition of Hazardous Material-
Properly disposition of hazardous materials is essential for safety, compliance, and environmental protection. ERP software for Chemical helps here in:
- Identification: Labelling and classifying materials per OSHA and GHS standards.
- Safe Storage: Proper tracking of material to ensure their safe storage.
- Regulated Transportation: Generate documents as per DOT standards with proper packaging labels.
- Responsible Disposal: Store all documents related to Partnership with certified companies for safe treatment or recycling.
- Employee Training: Maintaining HMIS/WHMIS, SOPs and other documents that ensure workers are trained in handling and emergency protocols.
- Compliance Records: Maintain documentation to meet regulatory requirements.
Effective hazardous material management safeguards people, the environment, and businesses.
Final Words-
Managing hazardous materials is a complex task for manufacturers to perform as even a small flaw could turn into a mishap. This is why ERP system has become a preferred choice for manufacturers that empowers businesses to enhance safety, reduce risks, and achieve compliance effortlessly.
Although adopting ERP software is crucial, selecting the right one guarantees your business’ success. Adopting an ERP software for chemical manufacturing like BatchMaster ERP is not just a step toward operational excellence, but a commitment to safeguarding your workforce, environment, and reputation. Contact our team of experts today, as they are happily assist you.