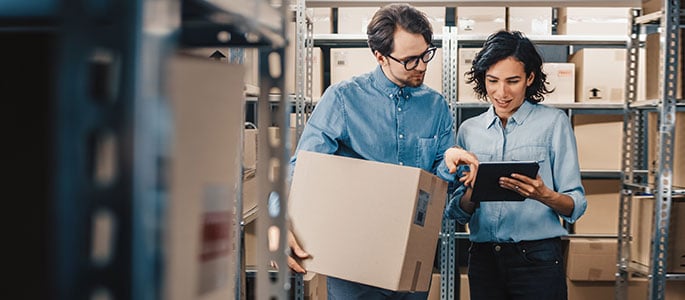
The main goal of any process manufacturing business is to carry its manufactured products smoothly from the initial phase, production phase, to the customer.
In executing this process seamlessly, it requires an effective and accurate Bill of Materials (BOM).
It is an integral component of the manufacturing process that keeps all the concerned departments together and provides the plan of how a product should be put together.
Being an essential part of the manufacturing process for the process manufacturing industries, BOM is used to link the formula with the finished goods, or the intermediates stored in the inventory.
The importance of Bill of Materials can be understood in a better way from a fact.
It’s, if the business goes to production with even a slightly inaccurate BOM that lacks any information or instruction, its consequences can range from wrong product manufactured or a completely dissatisfied customer.
Hence, it is of utmost importance for the businesses to understand what Bill of Materials is.
Also, how it works to ensure timely and efficient production of goods, as well as overall business efficiency and profitability.
What is Bill of Materials?
Wikipedia defines a Bill of Materials as a list of the raw materials, sub-assemblies, intermediate assemblies, sub-components, parts, and the quantities of each needed to manufacture a product.
A BOM may be used for communication between manufacturing partners or restricted to a single manufacturing plant.
It is often tied to a production order whose distribution may generate reservations for components in the bill of materials that are in stock and requests for components that are not in stock.
In simple words, a Bill of Materials is required to define how an item is manufactured from top to bottom. It is a structured list of all the components that make up a product or assembly.
The list is made up of the material number of each component, together with the quantity and unit of measure.
Also, the components can be raw materials, semi-finished products, or ingredients. BOM can be single level and multi-level.
For example, finished material would contain semi-finished materials as components, which in turn would contain raw materials as components in next level.
BOM also includes detailed instructions on how to assemble the product right from the idea through to the finished product ready for shipping – including all the packaging and instructions, etc.
A well-defined BOM helps companies with:
- Planning for purchases of raw materials
- Estimation of the material costs
- Complete inventory control
- Tracking and planning material requirements
- Maintaining accurate records
- Waste reduction
Talking particularly about the process manufacturing industry, the packaging of finished goods is often done keeping the convenience and the requirements of the end consumer in mind.
These options may range from a small 200 ml bottle to bulk containers for mass consumption.
In this case, with the help of BOM, you can link formula, labour, overheads as well as packaging materials with the finished good to govern the production process.
[wp-video-popup
video=”www.youtu.be/ukiGrRlg0ZM”]
Handling BOMs:
Companies normally have many BOMs defined for their different products. And, with the growing demand of multiple packaging by the consumers these days, this number is increasing.
Normally companies have one BOM per product, so greater the number of packaging available for a product, greater would be the number of BOMs.
Managing such many BOMs, their revisions and tracking of their versions can be confusing.
Today, Process manufacturing ERPs are built to handle complex multi-level BOMs with complete ease. An ERP solution’s BOM module can do tasks such as:
- Defining n number of BOMs
- Managing their revisions
- Tracking their numerous versions
- Returning to prior versions, and
- Analysing their costs, etc.
Mentioned below are some features of BOM module of a Manufacturing ERP:
- Allows one formula to be linked with multiple BOMs
- Describes intermediate and Finished BOMs
- Flexibility to define Fill Level in desired unit of measurement
- Serves multiple packaging options
- Separately analyses formula and packaging costs along with labour and overheads too
- Provides drill down and BOM where-used information
- Different BOM types like Fill, Assembly, Container BOMs, etc. to meet different packaging needs
- BOM report to classify the top assembly items, assembly types, and status of the BOM components associated with the formulas
- Proves beneficial for both Process (Formula BOM) and Discrete (Assembly BOM) Manufacturing
- Delivers full view of the BOM hierarchy
- Single BOM allocation with multiple formulas
We are Here to Help-
For the process manufacturing industries, one specialized manufacturing ERP which comes with a comprehensive BOM functionality is BatchMaster ERP.
If you would like more information on this subject, including BatchMaster Manufacturing ERP please contact us.
For more information on our different ERP offerings, visit our website.