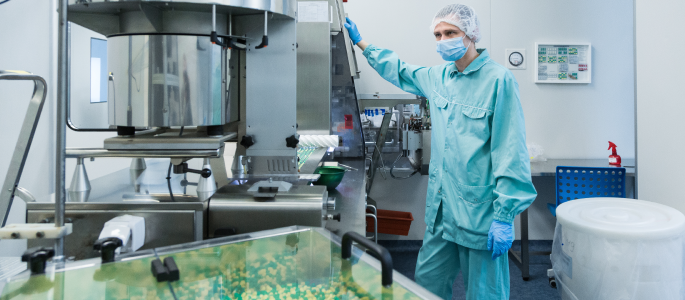
COVID-19 has proved to be the biggest challenge in modern times – particularly from the perspective of pharmaceutical manufacturing industry.
Not only has it compressed the pharma go-to-market-timeline, prompting the manufacturers to develop new COVID-19-related medicines and vaccines in record time, but also forced them to ensure that the production of non-COVID-19 segment remains unaffected.
While doing so, the manufacturers need to ensure that rigorous regulatory compliance protocols are being maintained.
And to ensure the same, the pharma manufacturers find it increasingly important to rethink their approach to ensuring production quality, and become more proactive with predicting the potential quality issues before they actually take place.
Sound quality management in pharmaceutical industry while ramping up the production is particularly important for the pharma manufactures, as incidents related to quality violations have already had an impact on millions of doses of just the COVID-19 vaccines.
So, the question is, how can the pharma manufacturers effectively manage rapid production processes while adhering to quality requirements?
By having an ERP-QMS combo
For any pharma manufacturing enterprise, majority of challenges, including the ones related to managing the production processes as well as quality, stem either from over-reliance on manual processes and data exchange, or a lack of integration and interoperability between the disparate enterprise resource planning (ERP) software, and quality management system (QMS).
The latter of the two mentioned above adversely affects the efficiency and effectiveness of the quality management processes, besides giving rise to data integrity-related issues.
For pharmaceutical businesses, there is a significant amount of data available that can be harnessed to improve quality during the manufacturing process and manage product quality complaints, as well as other aspects of quality including pharma quality assurance, and quality control.
Data can also be used for early detection of systemic issues, identifying bottlenecks, and predicting future quality performance. But to reap the full benefits of the abundant data available from across the enterprise, pharma businesses need to integrate their rigid systems.

This collaboration between its enterprise and quality systems offers a way to better partner between quality, and manufacturing. It essentially:
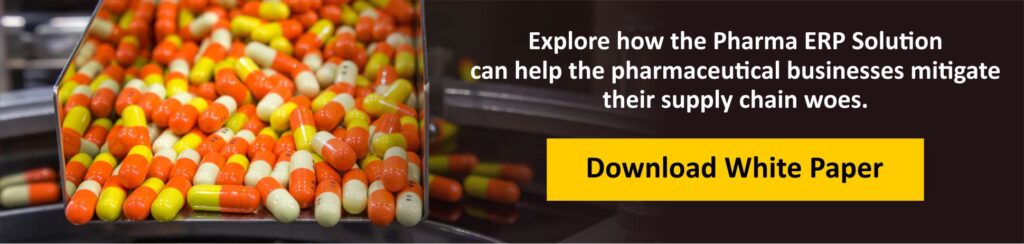
– Allows protecting data integrity
The integration between the quality systems and the enterprise system increases efficiency and reliability in quality control.
The combination of the two systems working in tandem makes initial results available during the production process, and reports and compliance documentation as soon as a batch is finished.
The electronic storage of data reduces the likelihood of errors.Â
Moreover, if the recorded production data goes outside the expected range, quality management receives an automatic alert.
And if the systems are cloud-based, all the stakeholders get access to the most up-to-date data.Â
– Allows defining QC tests, inspection plans, and checklists
By having good ERP software in place, pharmaceutical manufacturers can define the inspection plans based on the inspection checklists.
This way, they can have a mechanism to determine what to inspect, how and when to inspect, and a basis for inspection.
The manufacturers can know post-inspection whether the item is within tolerance or can be rejected if it fails to meet the defined standards.
This way, quality is ensured as only those items are used for production that meet the set standards.Â
An ERP also allows creation and storage of QC tests in its quality libraries, where the parameters for each QC test for a specified item or item group can be defined.
It also enables manufacturers to manage the records of all the tests, and accept or reject the product based on inspection result, thus ensure quality at all stages of production process.Â
– Allows rework on products in WIP
An ERP further allows pharmaceutical manufacturers to capture QC tests, and make changes in the ongoing production process if there’s any discrepancy.
Based on the result of the QC test, the users can rework on the product in WIP by adjusting certain batch job formula values and equipment settings.
This ensures that the quality remains uncompromised even when the production work is in progress.
– Allows maintaining compliance
The integration of an ERP system and a QMS system makes quality management in pharmaceutical industry a cakewalk for the manufacturers by providing full, out-of-the-box compliance as standard.
The manufacturers can meet regulations such as FDA 21 CFR Part 11, and also the requirements of current Good Manufacturing Practice (cGMP).
The features of the two systems enable manufacturers to meet compliance requirements more easily and efficiently.
– Simplifies operation workflows
Since pharma manufacturing involves batch manufacturing, the stakes are higher, for a single error can ruin an entire batch, resulting in significant loss of money, time, raw materials, and sometimes, even in fines, lawsuits, and damaged reputation.
Effective batch control that an ERP provides is essential for the same, which allows manufacturers to easily control the process and optimize production.
– Manages NC and CAPA activities
The ERP-QMS combine also allows the pharmaceutical manufacturers to manage non-conformance (NC) and corrective action preventative action (CAPA) activities.
With it in place, the events of NC are immediately identified so that the corrective action can be taken promptly to minimize the damage or loss.
The manufacturers can respond swiftly to any current/potential product quality risks, thus ensuring quality.Â
– Improves the life of equipment
To ensure effective quality management in pharma industry, alongside managing the rapid production processes, pharma manufacturers, most importantly, need to ensure that the production processes run uninterrupted.
This can be done by maintaining and improving the life and uptime of their machinery, because when equipment breaks down or underperforms, companies lose valuable resources such as money and wasted production time.
By having a pharma ERP software in place, the manufacturers can have an effective predictive maintenance program in action.
It allows them to know when equipment need maintenance work so that the production batches can be scheduled accordingly.
By having a robust ERP system, the manufacturers can eventually avoid downtime, and errors in production, thereby managing production while meeting the quality needs.
Conclusion
In today’s challenging business environment that involves cut-throat competition, the pharma manufacturers need to make efforts to manage production ramp-up, comply with the stringent quality as well as compliance regulations, and offer safe and quality products to their customers.
The right blend of technology can help them achieve these objectives.
Over the last 30+ years, we at BatchMaster have worked with some of the leading pharmaceutical manufacturing companies around the world to help them manage their business operations on the whole, flag potential issues, and improve productivity in quality and operations.
To know how our pharma ERP, as well as QMS software solutions, can help your pharmaceutical manufacturing business scale up the production processes while efficiently meeting the quality requirements, and manage pharma quality assurance, quality control, and other aspects of quality management, contact us today. Our team of experts would be happy to help you with a demo or a no-obligation consultation.